In the process of performing electrical wiring, every master is necessarily faced with such an activity as connecting sections with a wire to each other. The most common electrical wiring fault is a short circuit. Also, a very common unpleasant occurrence is a circuit break, most often it happens at the junction of the wires. These connections are made in and mounted in the plane of the wall or on its surface. Often inside these boxes, there are wire connections that lead to the automatic distribution panel, as well as wires that go to outlets and lights. Another wire can be laid parallel to them, which connects the boxes.
Terminal Blocks
The use of this switching option is the most popular due to the minimal labor costs for installation and compliance with all standards. A separate advantage is the ability to connect wires of different sections and materials. These days, the market for electrical materials is crowded with various products, but these terminal blocks are undoubtedly the best sellers.
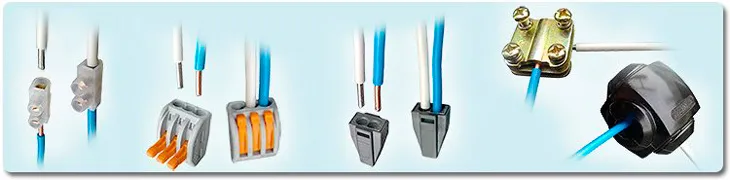
Types of wire terminal connections
Terminal clamps allow you to eliminate contact between wires made of different materials in the connection of wires. Today, the leaders in the field of electrical connections are 3 types of terminal blocks:
- Spring type.
- Screw type.
- Knife type.
The pads are mainly made of brass. They consist of assemblies of 2 or more terminals. Some varieties are filled with a specialized gel to protect against external corrosive influences. They differ from each other in: the diameter of the connecting cores, voltage and current.
Currently, this type of wire connection, such as ordinary twisting, has begun to fade into the background. To ensure reliable contact at the junctions of electrical wiring, specialized connecting terminals are used, which are called terminal blocks. There is a huge variety of such pads on the modern market in our country. They differ from each other: in price tag, design and some performance features.
The design of the pads is identical. It consists of the body itself, inside of which there are special cells, and inside these cells there are already brass tubes with several threaded holes.
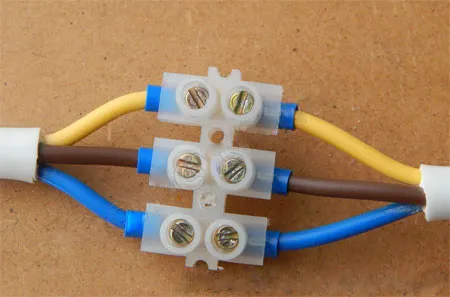
The tubes themselves come in different sections; they are selected according to their diameter, corresponding to the cross-sectional diameter of the wires themselves.
Terminal blocks are used in a wide variety of places. An example would be the way to connect an ordinary chandelier in an apartment; it is connected to short conductors sticking out of a hole in the ceiling.
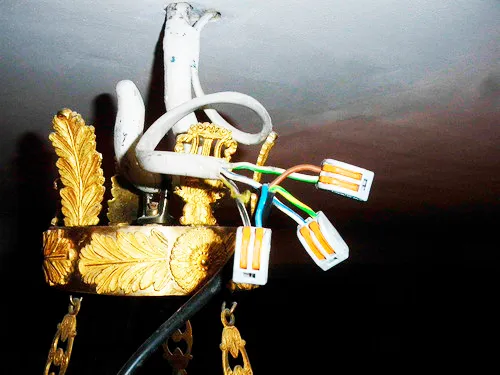
This method is often used to connect wires that are broken and located in the wall. Often such conductors are not long enough for subsequent connection in another way.
Advice from the expert: “The pads should be located directly in the junction box. Their placement inside the plaster is strictly prohibited!”
Although this connection is inferior in reliability to the connection, it is ultimately more convenient and requires minimal time investment.
The main advantage of terminal blocks is the fact that they can connect aluminum and copper conductors. To eliminate the oxidation process, in this case only one wire is passed through the clamping screws, contact between the wires is completely excluded.
WAGO terminals. Design features and differences from other terminals.
The WAGO company (WAGO Kontakttechnik GmbH & Co. KG) was founded in 1951 in Germany. She began her production with the development and implementation of spring terminals, in which she was very successful. To this day, the company is engaged in the production of this electrical equipment and finds only positive reviews in the electronics and electrical engineering market.
1973 marked the beginning of the production of the first small-sized terminal blocks. Then these products were patented, and production began to increase. Today, VAGO is a world leader in the production of spring terminals and other connectors necessary for the installation of electrical wiring.
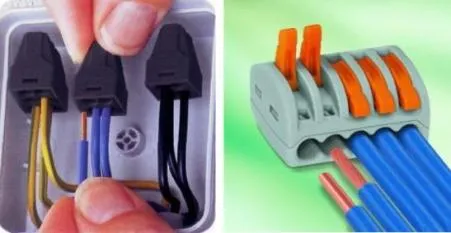
The main advantages of spring terminals are:
- High level of vibration resistance of the resulting connection.
- The contact point itself is securely fixed thanks to the spring pressure. This feature eliminates the plastic deformation of the metal.
Terminal blocks for connecting wires from WAGO have passed all types of international electrical installation certifications. They can be used when reconnecting wires. The terminals are also equipped with technological holes for connecting the probe to a thin support rail. The product does not require the use of special tools.
The terminal group includes both springs and thin support bars. These busbars are made using copper tinning. This fact protects against corrosion and increases the contact area of the conductors.
The springs have a flat shape and are made of austenitic steel. Thanks to this, they have increased elasticity.
The housing for these terminals is electrically insulating. It is made from modified polyamide and polycarbonate. These substances have high resistance to ignition, and self-extinguishing, and are resistant to fuel lubricants and other external influences.
Connecting wires using terminal blocks
Choosing a block for connecting wires is a responsible action. It is necessary to pay attention to the strength of the current that will subsequently flow through this product. It is also necessary to purchase the required number of mounting terminals.
The process itself is not a complicated procedure; even amateurs can carry it out if they have the initial necessary knowledge and skills.
The block is selected according to the size of the cell, all excess sections are cut off. Most often they are made with terminal blocks.
Having previously removed the conductors from the connecting ends, the wire cores are inserted into the terminal cells and all conductors are clamped using screws. The surface of the core must be cleaned. A slight amount of force is allowed when tightening the screws.
In the case of connecting aluminium conductors, the screws are tightened very carefully, without much pressure. This is done to avoid breaking the wire and deteriorating the contact in the future since this metal has high fluidity when heated.